[ad_1]
High-value real estate dominates Miami’s coast, where luxe hotels, stretches of retail and apartment complexes come with waterfront views. Along the Atlantic Ocean and Biscayne Bay, however, high value also means high risk. Enter seawalls: a complex climate solution undergoing major innovation.
Seawalls are “just simply to keep the water out where the water belongs and keep the people or everything else in where it belongs,” said Philip Parker, an architect and an adjunct associate professor in Pratt’s Graduate Architecture and Urban Design department. “So, the wall becomes this massive separator.”
Historically, seawalls have been the go-to solution for flooding in the United States. Nearly every waterfront property in the nation — with the exception of beaches — has a seawall, said Anya Freeman, founder and CEO of Miami-based Kind Designs, which creates 3D-printed seawalls that mimic natural reefs.
But seawalls have long-standing environmental, financial and efficacy problems, and have met pushback in recent years. “Can seawalls save us?” The New Yorker asked in November, while “In Florida, Seawalls Are Not the Answer,” The Tampa Bay Times declared in May.
Plus, seawalls may not be able to outlast incremental sea level rise, nor address massive storm surges. In 2021, plans from the U.S. Army Corps of Engineers to raise walls in Biscayne Bay to a height of 20 feet sparked widespread opposition and were ultimately abandoned. (For reference, the City of Miami requires a minimum sea wall height of 6 feet, with height requirements to rise in conjunction with sea levels.)
And, yet, in New York City, the Army Corps of Engineers proposed a $52 billion effort that would introduce seawalls and gates across New York Harbor.
Because, as sea levels rise, the walls that hold in the water are an important piece of the resilience puzzle.
So, seawalls are both necessary and flawed — which highlights the potential for new designs and technological innovation, such as Kind Design’s “living seawalls,” as Freeman calls them. In fact, seawalls have not been updated in about 100 years, said Freeman — so improving what can be improved is a good place to start.
Breach read
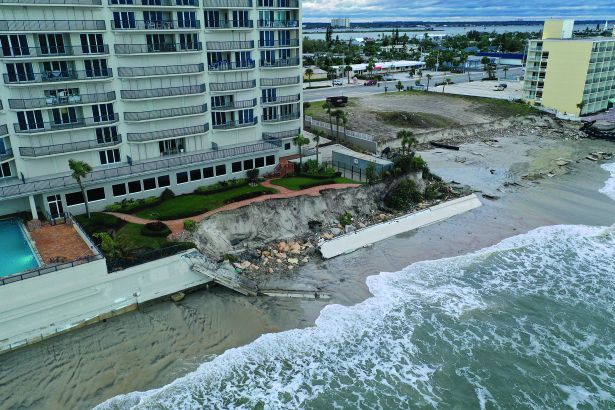
Traditionally, Miami’s seawalls were built to keep land in, water out, and, in some cases, offer a place to tie up boats, said James Murley, Miami-Dade County’s chief resilience officer. Murley made the distinction between traditional seawalls and the walls proposed for Biscayne Bay in 2021. Those walls, he said, were bigger and more expensive storm surge walls, designed to protect communities from a 15-foot storm surge pushed inland by a hurricane.
Such terms, however, are often referred to interchangeably, and generally serve similar purposes. Contrary to their names, seawalls and similar flood protection systems — storm surge walls, levees, floodwalls — can neighbor any body of water. These infrastructural mechanisms are not exactly the same but vary in design. However, they epitomize similar strategies for resilience.
Often made of concrete, or sometimes with steel or other standard materials, traditional seawalls don’t exactly enhance nature’s beauty. Their harsh, flat appearance became a major point of contention in the Biscayne Bay proposal; not only would 20-foot walls have looked “hideous” — as one source told The Guardian — but they would have also inhibited direct access to the water.
Herein lies a conundrum for commercial real estate. Unsightly seawalls can impact a building’s value, disrupting views and aesthetics alike, despite simultaneously protecting that real estate. “It’s such a challenge to figure this puzzle out because even though we have a hurricane season every year, we don’t get a storm surge every year,” said Murley. “But the value of the real estate is why we even contemplate [it].”
New seawall designs, however, may reconcile some seawall contradictions, at least in regard to aesthetics. Kind Designs makes panels that are more natural and textured in appearance, though they’re still made of concrete.
Of course, it’s what’s on the inside that counts — but, in the case of Miami’s seawalls, the infrastructural benefits may not be as solid as they seem. Just as it’s risky to forgo flood protection, it’s equally risky to build a wall, and then rely on it, especially for a city like Miami that’s built on porous limestone.
“Basically, the water will forever flow under any pilings you drive to build the wall on top of,” Peter Waggonner, director of public policy for economic development agency Greater New Orleans Inc. (GNO), said about Miami’s limestone origins. This means Miami’s seawalls can’t necessarily prevent an upward movement of water.
For comparison, New Orleans — which predominantly uses levees for coastal flood protection — was built on organic soils and clays. “You can build a levee and the water won’t necessarily flow under forever,” said Waggonner. “So it really depends on your sub-surface to determine whether a floodwall is right for your community.”
Regardless of composition, there’s no guarantee that any one wall will yield success. Instead, effectiveness hinges on a slew of factors, including the local tides, the chance of a hurricane and construction quality. During Hurricane Katrina, outfall canals failed from poor engineering.
“The whole thing about a seawall — the reason why they all fail eventually — is you could have 20 miles of seawall surrounding New Orleans, and there’s one breach and it’s over,” said John Shapiro, the former chair of Pratt’s Graduate Center for Planning and the Environment and previously of planning consultancy Phillips Preiss Shapiro Associates.
Creature comforts
Even if a flood protection system holds up, another problem presents itself in the long term.
“That is the coastal erosion crisis,” said Waggonner. “Previously and historically, and century upon century, the river deposited its sediment to build coastal Louisiana.” Now that the river is leveed, it can no longer deposit that sediment and instead funnels it out and into the Gulf of Mexico.
On a broader scale, erosion occurs when water comes in and hits the seawall. Then, it goes back out. “When it does that, it produces what’s known as scour,” said Parker. “It hits the wall and it comes down, and it pulls across the bottom and tears everything up.”
Likewise, traditional seawalls are flat, so sea life can’t easily attach. Consequently, organisms leave the area, said Freeman. Without sea creatures present to consume toxins, the water’s quality drops by 50 percent within one year of the seawall’s installation.
In New York City, pollution is especially a point of conversation, as it’s not clear what happens behind the wall to pollutants, said Shapiro. Amid the seawall conversations, there’s concern about re-polluting Queens’ Jamaica Bay and overturning the progress of the last 50 years.
However, 3D-printed seawalls can mimic marine habitats, responding to sea life rather than forcing it away, and can do so in a more expedited manner than traditional designs. As sea levels rise, building walls or raising pre-existing ones — whether to 20 feet or to the latest minimum requirements — becomes all the more urgent. If it takes 10 or more years to build a seawall, as is often the case, the lifespan of that wall shrinks — and the sea waits for no one, said Shapiro.
“The sea rise is not saying, ‘Oh, we’ll wait until you’re done,’ ” he said.
In Miami, it takes two years to get a seawall permit, said Freeman, largely due to their impact on the environment. Counties mandate environmental mitigation, so if a property plans to put in a traditional seawall, it has to mitigate habitat destruction by building another habitat.
Kind Designs, however, is working on certifying its seawalls as self-mitigating, which would counteract some of these temporal barriers while simultaneously benefiting the sea life.
Splitting the check
Seawalls are expensive, thanks to a labor-intensive construction method. Kind Designs sells its seawall slabs for $30 per square foot, similar to traditional panels. However, because its panels are 3D-printed, the company said the production process is far less intensive and expensive.
Public projects are, of course, funded by the public. The standardized cost share for Army Corps of Engineers projects is divided into 65 percent federal and 35 percent local funds. The pattern holds true across the country, from levees in Louisiana to the design and construction of resilience projects in San Francisco.
Usually, communities will have to pay, at least partially, for a flood protection system’s maintenance. In Louisiana, part of this payment is already fulfilled via property taxes. “Hotels, and these major hospitality and major industry and commercial establishments, all pay property tax, and they pay into the system that funds the operations and maintenance already,” said Waggonner.
If someone owns a house on the water, they must pay for the seawall, whereas the government covers the cost for locations like public parks, said Freeman.
Further up the East Coast, much of New York City’s shoreline is publicly held, muddling seawall finances as well as agency for owners of coastal real estate. “There’s a tremendous amount of discussion and regulation,” said Parker. The decision for a New York seawall brings in myriad voices: municipalities, the Army Corps of Engineers, legislation like the Clean Water Act, and so forth.
Modern models
Given the intersecting complications of seawalls, new approaches have been developed to modernize tradition and meet the demands of the current climate. “The seawall from Galveston, Texas [designed 100 years ago] is exactly the same seawall that we were still putting in the water today in Florida,” said Freeman.
Freeman’s 3D-printed seawalls mirror traditional walls via structure, installation method, reinforcement and materials. However, Freeman uses nontoxic concrete for seawalls that can be installed via local construction companies, and they don’t require any special treatment or equipment. The wall also collects data through built-in sensors.
Kind Designs can print 10-foot living seawall panels in one hour — a process that would take about a day with conventional seawall molds, according to the startup. In addition to lowering the production cost, this method allows Kind to incorporate design elements that evoke natural reefs, which attract sea life.
“When you start to build a more complex surface, then marine life can attach to that,” said Murley. “When you’re not experiencing storm surge, you’ve got a marine environment that’s helping you keep the water cleaner; you have water-quality benefits and other things that are desired by the communities.”
Kind Designs emulates the design of mangrove root — a natural marine habitat in Florida — into the face of its seawalls, so they create both 3-foot caves where sea life can hide from predators, and small, special textures for smaller organisms to attach.
“It functions as bio concrete, it strengthens the wall, it repairs cracks and it sequesters more carbon every year as more organisms attach to the seawall,” Murley said.
As for the market for new seawalls, many places that need a seawall already have one. About 90 percent of Miami Dade County’s shoreline — where urban areas are behind it — has seawalls that were built over decades, said Murley.
Miami-Dade County has building code requirements for the height, structure and purpose of those walls. “But if you choose to leave your shoreline natural, or to allow mangroves to be planted there or naturally grow there, that’s perfectly legal,” he said.
The government likewise does not require existing seawall owners to rebuild seawalls to new height regulations, said Murley. Yet even without government-mandated height upgrades, seawalls fail roughly every 50 years, thanks to issues with rebar. To reinforce a seawall’s concrete, steel bars — known as rebar — go inside the material. When underwater, that rebar rusts and consequently expands, eventually popping the seawall’s concrete. This damages the seawall and often results in structural failure.
That malfunction, coupled with rising minimum seawall heights, opens the door for new designs.
Miami is actively exploring such options. Different municipalities within Miami-Dade County — North Bay Village and Miami Beach, for example — are conducting pilot studies of next-generation seawalls.
In October, Kind began to install a 120-foot seawall in Miami Beach on Pine Tree Drive. The area will be the first to install Kind’s design on a public space, reported NBC Miami.
“If you can do something like [Kind] cost-
efficiently, with minimal impact and the same efficacy, that’s so awesome,” said Waggonner.
Parker and a team of sociologists, economists, engineers, academics and other experts have also proposed a 3D-printed seawall project through a National Science Foundation grant focused on remaking urban shorelines. They are currently developing a prototype within the design system.
Specifically, Parker and his colleagues are reconfiguring how a boundary on an urban shoreline gets made with varieties of novel concrete; where that boundary is located; and how people and other creatures interact with it, said Parker. Like Freeman’s design, Parker’s proposed project is not flat. Rather, it also includes pockets and spaces, and can change wave attenuation.
Nor is the design one-size-fits-all across geographies. Rather, Parker and his colleagues are considering geographic differences in hydrology, life, political associations and so forth. By varying the wall’s materials, composition and form, among other factors, the new design can speak to a geography’s specific needs. “What we’re designing is not a wall but a system: a way in which we can actually use advanced computation to make variations in the edge and implement those in different places,” Parker explained.
On the other side
Even when better designed, seawalls may only be able to go so far. Climate resilience calls for a systems approach, said Pratt’s Shapiro, and although he gets excited about creative ideas, he’s reluctant to embrace any one solution, no matter how innovative.
“To an engineer, this is an engineering problem,” said Shapiro. “To an architect, this is a design problem … the wall always is popular with politicians because it’s simple.”
Seawalls are therefore just one part of the equation. Interior adaptations — green infrastructure, stormwater parks, water storage tanks and the like — can further help communities manage water.
“You start looking at ways to flood-proof the buildings, even elevating some single-
family homes,” said Miami-Dade County’s Murley. “Look at what are called nature-based features along the shoreline, which don’t keep the water out like the wall did but do reduce the energy and therefore the potential for damage to the expense of real estate.”
“Ideally, there would be multiple barriers of defense,” said Waggonner of New Orleans. “But there is a way to spread the risk and not put all your money into a seawall that might have a tiny chance of failure.”
Brooklyn’s Red Hook, for instance, faces five different flood threats that include rising seawater, storm surge and rainwater. A seawall, however, addresses only surge and sea rise, said Shapiro. Unless its sewer systems are redone to pump out water from storms, Red Hook will likely still flood.
However, some places — including Red Hook — need some sort of flood protection system, whether it’s a seawall, a berm or even the edge of a linear warehouse, as has been developed on the waterfront in Hamburg, Germany. This imminent need circles back to all those Army Corps of Engineers proposals. In New York City, the corps has one order: to stop another Hurricane Sandy. A wall offers a neat and direct response to that demand.
Storm surge walls are built to protect from storm surge, said Murley, but don’t do anything for high tides or rain events.
“People want to think that they’re out of danger,” said Shapiro. “And so what walls do is create the feeling of protection.”
Then again, as Shapiro says, “No one wins by being Chicken Little.”
[ad_2]
Source link